28.February.2025
Everything You Need to Know About Cement Board Types and Applications(Large-Scale Construction)
Cement boards have transformed contemporary construction, delivering strength, adaptability, and reliability across a wide range of uses. From towering tall buildings and expansive shopping malls to hospitals and industrial facilities, these boards serve as an excellent choice for large-scale projects that demand durable materials capable of withstanding demanding environments. In this blog, we'll look into the various types of cement boards, their characteristics, the manufacturing process, and their role in large-scale construction endeavors.
What are cement boards?
Cement boards are a type of engineered board that combines a distinctive set of properties, making it suitable for a wide array of applications. It is composed of a composite material created from either cement-bonded particle boards or a mix of cement, cellulose fiber, silica, and other fillers. Another variation of cement board is produced using cement and cellulose fiber, which acts as reinforcement.
The strength of the board comes from its cement-bonded particles, mainly processed wood flakes, and cellulose fibers used for reinforcement. Cement serves as the binding agent, providing structural integrity while holding the wooden particles and cellulose fibers together.
In the world of construction materials, the cement board plays a pivotal yet understated role, offering strength, resilience, and versatility. With its exceptional qualities, cement board is widely utilized in numerous applications. While often overshadowed by more prominent materials like concrete and steel, the cement board delivers a unique combination of attributes and uses that make it indispensable in modern construction practices.
What Are the Different Types of Cement Boards?
Cement boards come in various types, each tailored to specific properties and suitable for particular applications. Common types include fiber-cement boards, high-density cement board wall panels, and cement-bonded particleboards. Let's take a closer look at each type:
Fiber-Cement Boards
Fiber-cement boards are composed of wood fibers, Portland cement, and sand. These boards are an excellent choice for outdoor applications such as siding, roofing, and cladding. They are specifically engineered to withstand harsh weather conditions, including heavy rainfall and intense sunlight. Additionally, they offer protection against water, fire, and pests, making them a highly durable option for numerous construction needs.
High-Density Cement Boards
High-density cement boards are made using cellulose fibers, Portland cement, and mineral additives. These boards are significantly more robust than some of the most critical structural elements, including floors, walls, and countertops. Their water-resistant properties, combined with fire and pest resistance, make them one of the safest and most reliable materials for construction projects.
Cement-Bonded Particleboards
As the name implies, cement-bonded particle boards are manufactured by combining wood chips or shavings with a cement-based material that binds them together. These boards are beneficial for housing construction or renovation projects, as they provide excellent insulation, helping to reduce heating costs. Their thermal efficiency makes them a practical and energy-saving choice for modern construction.
Cement boards offer a versatile range of options, with each type bringing unique benefits, ensuring their suitability for diverse construction applications.
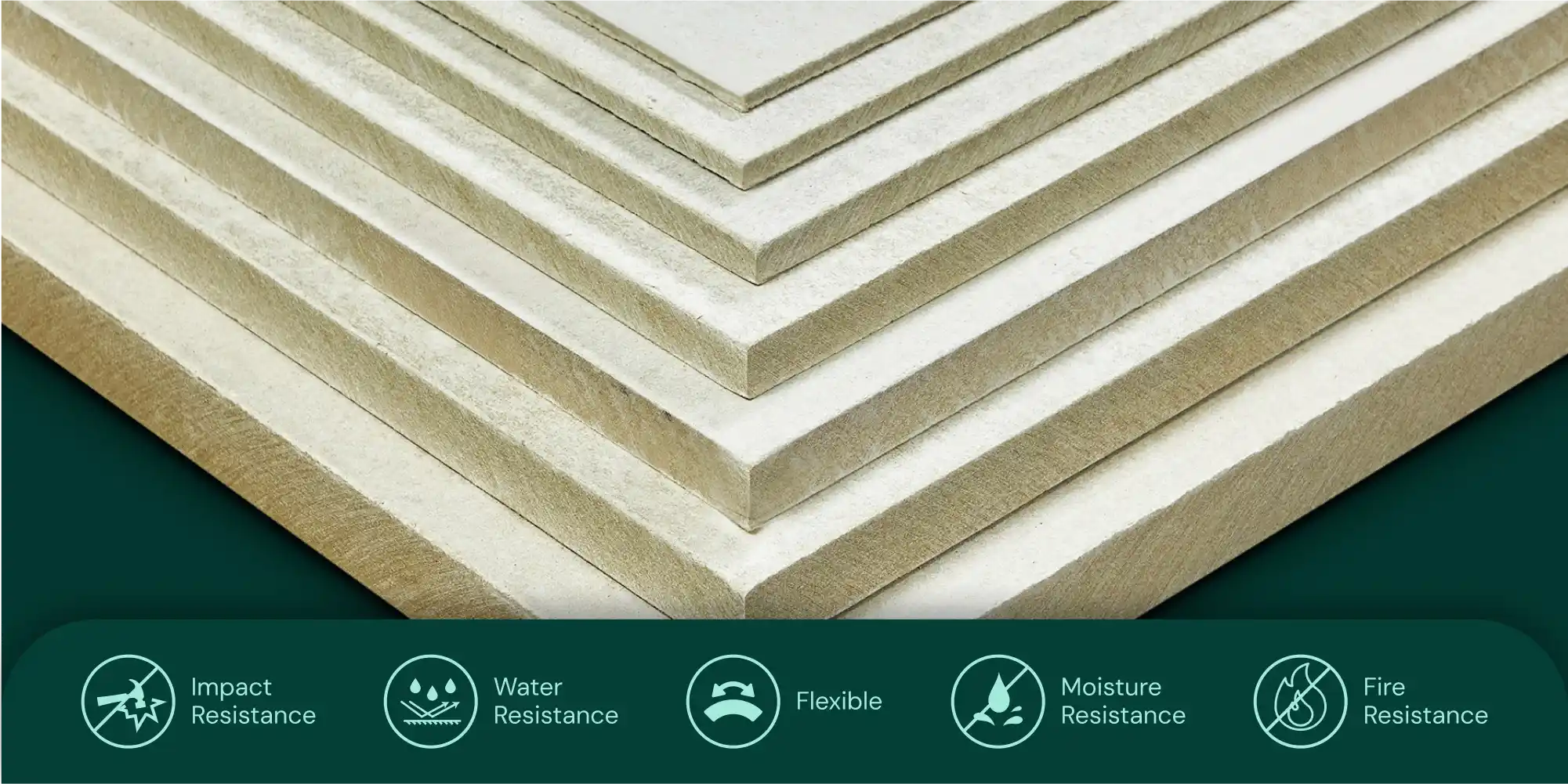
Characteristics of Cement Board
- Strength and Durability: Cement board is known for its remarkable strength and long-lasting durability, making it perfect for applications that demand structural integrity and resistance to impact, moisture, and fire.
- Moisture Resistance: The cement board's outstanding moisture resistance makes it ideal for use in damp environments such as bathrooms, kitchens, and outdoor areas.
- Fire Resistance: Cement boards are naturally fire-resistant, offering enhanced safety and protection, especially in areas with higher fire risks.
- Dimensional Stability: Cement board maintains its form and size over time, resisting warping, swelling, or shrinking even under harsh environmental conditions.
- Versatility: Available in a variety of thicknesses and sizes, the cement board provides flexibility in design and application. It can be easily cut, shaped, and installed to meet the specific needs of any project.
Manufacturing Process of Cement Board
- Raw Materials: Portland cement, cellulose fibers, silica sand, and water are the key components used in producing cement boards.
- Mixing: These raw materials are carefully measured and blended to create a uniform slurry.
- Forming: The slurry is either poured onto a conveyor belt or into molds, where it is evenly distributed to create a thin layer.
- Pressing: The sheets are then passed through rollers or presses to extract excess water and compact the material for strength.
- Curing: The compacted sheets are cured under controlled conditions, allowing the cement to hydrate and the boards to solidify.
- Finishing: After curing, the cement boards may undergo further processing, such as sanding, cutting, or coating, to achieve the required surface finish and appearance.
- Quality Control: Finally, the finished boards undergo stringent quality checks to ensure they meet industry standards and specifications.
Applications of Cement Boards in Large-Scale Construction
- Wall Systems and Partitions
Cement boards are used to construct partition walls in large-scale projects such as hospitals, schools, and office complexes. These boards provide excellent acoustic insulation, ensuring privacy and noise reduction. Fiber cement boards are particularly favored for this application due to their lightweight and easy installation. - External Cladding
Exterior cladding is a critical aspect of construction, as it not only defines the building's appearance but also protects it from environmental factors. Cement boards, especially fiber cement boards, are widely used for cladding because they can withstand extreme weather conditions and resist mold and mildew. - Flooring Substrate
Flooring must endure high foot traffic and weight in large-scale buildings like malls and airports. Cement boards serve as an excellent substrate for tiles, stones, and other heavy flooring materials, providing a stable base that resists cracking and warping. - Roofing Underlayment
Cement boards are often used as an underlayment for roofing systems, especially in regions with high humidity or frequent rainfall. Their water-resistant properties ensure durability and structural integrity, even under challenging conditions. - Fireproofing Applications
Fire safety is paramount in large construction projects. Cement boards, known for their non-combustible nature, are frequently used in fire-rated walls and ceilings. This application is crucial in facilities like data centers, high-rise buildings, and industrial plants, where fire resistance is critical. - Wet Areas and High-Humidity Zones
For wet and humid areas, such as bathrooms, locker rooms, and kitchens in commercial or residential buildings, glass-mat cement boards are the preferred choice. They prevent water damage and inhibit the growth of mold and mildew, ensuring longevity and hygiene.